Air up
Resource-efficient 3D printing of functional and adaptive integrated lightweight structures for use in building construction
Period:
10.2023 – 09.2024
Prof. Dr.- Ing. Oliver Tessmann | FB 15, Fachgebiet Digital Design Unit
Dr.-Ing. Dieter Spiehl | FB 16, Institut für Druckmaschinen und Druckverfahren
---
Project description:
In the “Luft nach oben” project, an innovative 3D printing process known as blow extrusion 3D printing was further developed in an interdisciplinary collaboration between architecture and mechanical engineering to produce resource-saving, hollow lightweight structures for the construction industry. The aim was to replace climate-impacting building materials such as concrete with material-saving plastic parts of the same volume and at the same time increase the functionality of construction elements. To accomplish this, thermoplastics were inflated with air during 3D printing to create hollow cross-sections. This enabled a material reduction of up to 85% compared to conventional, solid components. The collaboration between the Institute of Printing Science and Technology (IDD) at the Department of Mechanical Engineering and the Digital Design Unit (DDU) at the Department of Architecture brought together robotic manufacturing, innovative 3D printing technology and parametric design. This made it possible to produce threedimensional components freely in design and on a scale relevant to the construction industry using robotic manufacturing. Two processes with different feedstock materials were tested: plastic pellets, which are inexpensive and allow a high throughput, and plastic filament, which enables multi-material printing. The key results include large-format demonstrators, which will be exhibited at the leading 3D printing trade fair formnext in Frankfurt, as well as a publication, which will be presented at the BE-AM symposium to a specialist audience from the fields of architecture, design, and construction. The participating institutes gained valuable insights into the further development of the process and robotic 3D printing, which will lead to a joint follow-up application. The collaboration also influenced education at TU Darmstadt through several theses, the employment of student assistants and a contribution to the “3D printing” lecture series.
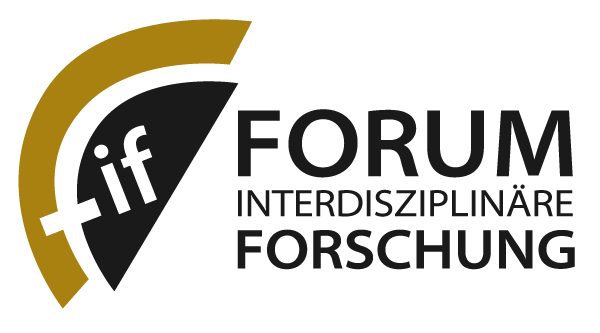